What goes into the process of troubleshooting a faulty motor, when are seeing signs that it is an electrical fault?
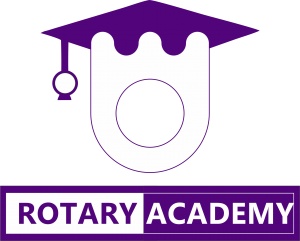
Part 11
Troubleshooting Electrical Faults 2
Watch the above animation in full, & Access other episodes now!
Signup for FREE to receive access >>>
Animated Video Tutorial Training Series - Part 11
Troubleshooting Electrical Faults (Part 2)
In troubleshooting electric motors, the most important issue is to find out the real cause of the coil burning, not to solve the problem by simply replacing the coil and burned components. Electric motor coils suffer from various damages, each of which has a different shape:
These are the most common problems in a three-phase motor:
- Loops in the coil that are shorted
- Grounding (the winding is shorted to the frame)
- Phase to phase connection
- Open circuit coil
- Burnt coils caused by single-phase electric motor
- Motor submerged in water
- Shaft voltage
short circuit
A short circuit is a common winding failure and requires re-winding or motor replacement. Shorted rings are caused by factors such as: creating scratches and cuts on the coil, sparking voltage with high amplitude, conductive pollutants, overheating of the coil, aging of the insulation and looseness and vibration of the coil wires. to be the greatest resistance to current in an AC motor is provided by inductive reactance. The resistance of the wire in a full phase is a very small percentage of the motor’s total impedance. Inductive reactance makes each turn of the winding coil significant in the amount of motor current. Each turn creates more inductive impedance than ohmic resistance.
A short circuit occurs when one or more turns of the coil are connected due to insulation damage between the wires. The resistance of the short circuit coils is reduced from the resistance of the entire phase coil, and as a result, the motor ampere will increase. When there are several short-circuited loops in one of the three phases, a closed-loop circuit is formed by the short-circuited loops. When the motor starts, the power lines cut the wires in a closed loop circuit.
Grounding (short circuit of the coil to the body)
When the motor is “grounded”, the winding is shorted either to the laminate core or to the motor body. This problem is usually seen in winding slots, where the slot insulation has been damaged. Water is the most common cause of winding grounding. If the ground connection is basic (irreparable), then rewinding or replacing the motor will be required. Some of the reasons for the failure of the groove insulation: overheating, pollutants with conductive components, lightning, aging of the insulation, pressure of the coils in the tight environment of the groove or coil head, creating hot spots due to the damage of the core sheets. due to previous failure of the coil) and vibration and excessive movement of the coil. Excessive movement of the coil is often caused by overheating and/or torque of the coil, which is due to reverse (connection) or disconnection. Electricity is generated momentarily.
Phase to phase short circuit
Phase-to-phase short circuit is caused by insulation failure in the coil head or in the slots. This type of error requires rewinding or replacing the motor. The voltage between the phases can be very high. When a short occurs, a large portion of the circuit winding is shorted. Both phase windings are usually melted, so the problem is easy to detect.
Among the reasons for failure between phases, we can mention pollutants, the narrow location of the coil (in the gap), aging, mechanical damage, and sudden spike voltages. The windings that form the poles of each phase are stacked in each three-phase motor.
Open circuit coil
One of the main reasons for the coil opening circuit is smaller than the size of the terminal board connections. Burnt connections in the motor junction box (terminal) are a sure sign of this problem. Open windings are also caused by short windings, short phase-to-phase connections, short earth-to-body connections, improper connections of internal coils to each other, severe overload, and damaged coils.
Upward errors require rewinding the motor coil or replacing it. The opening circuit of the winding has different indications
Winding burning due to single-phase operation
When one phase of a three-phase power supply is opened, the power becomes single-phase. If this happens while the engine is running, the power output will be reduced by almost half. The engine continues to run, but can no longer restart on its own. It will be like a single-phase motor whose starting coil is not excited and therefore has no rotating magnetic field to start it.
Motor submerged in water
If a three-phase motor is submerged in water but not excited, it probably won’t need to be rewound or replaced. It will be enough to clean and dry the coil through heating in the oven. The engine should be opened as soon as possible. If the engine has bearings, the bearings must be replaced. If it has a sliding bearing (bush), the oil-absorbing materials will cause rust or pitting of the shaft or bearing. Replace the lubricant immediately. If the engine has an oil tank and an oil ring, the tank must be completely cleaned. The windings should first be tested with an ohmmeter. A wet winding should never be subjected to a test voltage that could spark through the wetted slot insulation.
Shaft voltage
When the motor shaft voltages increase from the insulating ability of the bearing grease, electric discharge currents are established in the bearing. As a result, it creates holes and unevenness in the bearing frame. The first sign of this problem will be the noise and overheating of the bearing, so that the bearing starts to lose its original shape and metal fragments are mixed with grease. and increases bearing friction. This problem can lead to the destruction of the bearing in a few months and the failure of the engine. Bearing failure is a costly problem that should be considered both in engine repair and engine downtime, so to help prevent it, measuring shaft voltage and bearing current is an important diagnostic step. Shaft voltage is generated only when the motor is energized and rotating.
Sparking creates holes and grooves in the middle of the bearing, which leads to increased vibration and eventually the failure of the bearing.
If you bought a new electric motor, these problems are all caused by malfunctions in the factory that need to be corrected. If the factory equipment problem is not corrected, the replacement engine can sometimes be immediately damaged. Accurate identification of problems that require motor removal or replacement is very important. All faults detected in the windings shall be documented and recorded. A history of factory motor problems categorizes the problems and the user can check which of the categories are problems that can be improved or even fixed completely.
For more information , please contact us.

Let’s Connect. We’ll call you at your convenience.